Encore Wire Sustainable R&D Center
LEED® Platinum R&D Laboratory with Innovative, Energy-Efficient HVAC System
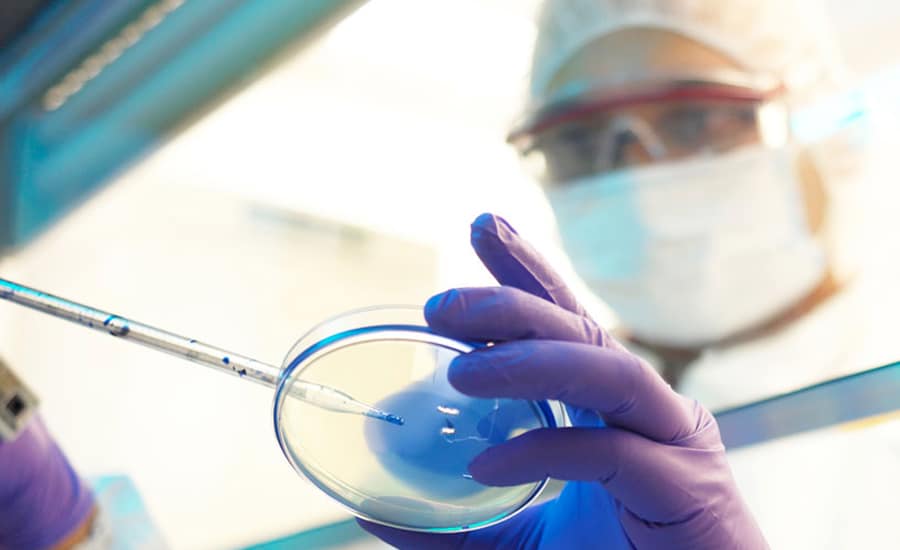
At A Glance
RESULTS: Air handler installation went smoothly as the uniquely configured unit was designed to fit within a penthouse on top of the building and took up less space than a conventional air handler. FANWALL TECHNOLOGY® offered significant energy savings that contributed to the lab achieving LEED® Platinum status.
When Encore Wire, a manufacturer of copper electrical wire and cable, was ready to expand, they knew they wanted sustainability to feature prominently in the design of their new building. They also knew that requirement would pose some challenges. The new Research and Development Center, located across from the company headquarters in McKinney, Texas, was slated to house a one-floor research laboratory that would perform a variety of analytical functions, including analytical chemistry, wet chemistry, and destructive testing. The president of Encore Wire, who is a big proponent of sustainability, wanted the building to achieve LEED® Platinum status. Ultimately, the HVAC system would need to provide a significant number of points towards successfully meeting that goal.
With special considerations like sustainability, space constraints, and redundancy, a custom HVAC solution was the best option. Ron Wyman, the engineer on the project, felt confident in his recommendation to use a Temtrol® brand. “I rarely use a catalogued solution,” he says. “And I trusted the air handling unit from Temtrol. I have used so many Temtrol custom air handlers in the past, I knew I could trust them.”
The team from Temtrol was up to the challenge, providing a FANWALL system with six fans using one variable-frequency drive, and an air handling unit that utilizes an enthalpy plate energy exchanger.
“FANWALL TECHNOLOGY provided the necessary performance right out of the box.”
Equipment
FANWALL TECHNOLOGY
A number of requirements made FANWALL TECHNOLOGY the ideal choice for the fan solution over a conventional one–two fan air-handling unit. Redundancy was especially important because of the critical nature of the equipment housed in the lab. Tests are often run for 72–96 hours at a time, and a power shutoff during that time would be disastrous. A FANWALL system offers the benefit of using an array of fans, so if one fan fails, the rest can still operate — meaning the system has very little chance of going down. Says Wyman, “We could lose two fans and still run the building without compromising anything.”
In addition, FANWALL TECHNOLOGY provided the needed energy performance to comply with ASHRAE Standard 90.1-2007 standards, something which, at only 18,500 cfm, was a challenge. Says Wyman, “Temtrol has a good reputation of producing really great products…and FANWALL TECHNOLOGY provided the necessary performance right out of the box. Many others couldn’t get the horsepower low enough to meet the project’s requirements.” Todd Clayton, Vice President – Facilities Engineering, agrees, saying, “FANWALL is a nice technology. Its quiet and it’s efficient. It certainly does the job.”
KEY POINTS
- The president of Encore Wire wanted the company’s new R&D center to achieve LEED® Platinum status.
- An air handler with FANWALL TECHNOLOGY and an enthalpy plate energy exchanger was used, providing significant energy savings.
- The air handler also met the reliability and performance requirements of the demanding laboratory environment.