Transamerica Pyramid
The Iconic Transamerica Pyramid Sets New Standard for Reliable and Quiet Systems
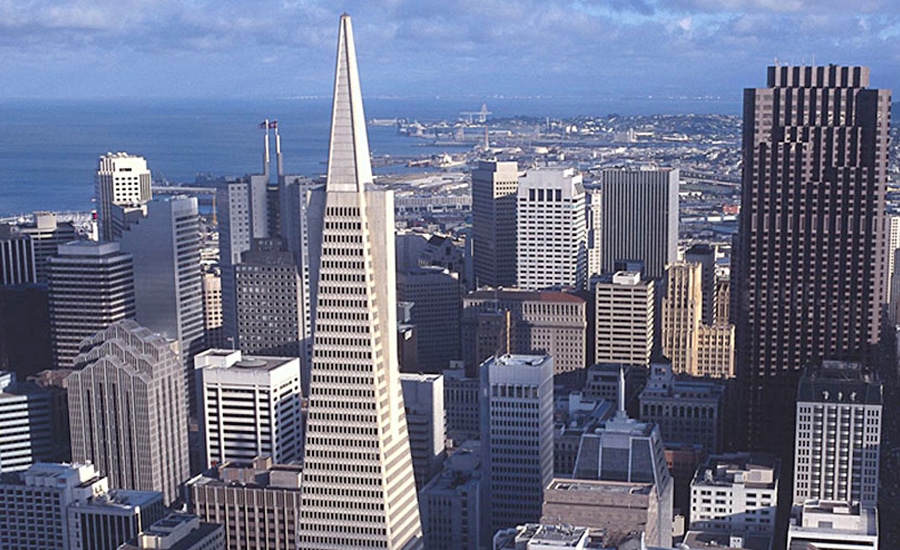
At A Glance
As integral to the San Francisco skyline as the Golden Gate Bridge and the Coit Tower, the Transamerica Pyramid has been recognized as an avant-garde building since the first cornerstone was laid in 1969. The iconic pyramid-shaped building, owned by AEGON since 1999, is the most recognizable within the larger Pyramid Center complex that encompasses an entire city block in the Financial District. Architects William Pereira & Associates chose the pyramid shape not just for its unusual look but also to meet a specific need: a pyramid casts a smaller shadow than a conventional high-rise building, allowing more light to filter to the streets below. At the time, that met the requirements of a special “shadow ordinance” in this foggy city on the bay. The building’s cutting-edge tradition continues today. Upgrades and retrofits have earned a LEED® Gold certification for the Transamerica Pyramid. And a recent upgrade to one section of the building’s HVAC system is equally inventive.
The aging air handler fans serving floors one to 18 of the building required continual maintenance because of their age. Building management sought a replacement that would cause minimal disruption to tenants, simplify and reduce costs for installation in the existing mechanical space, contribute to energy efficiency, and provide redundant operation.
Replacing the old housed fan with a new one was quickly ruled out. It would’ve required extensive demolition and reconstruction and would have disrupted tenants. Instead, AEGON opted to replace the old fan with FANWALL TECHNOLOGY, a modular fan system introduced in 2004 by Huntair, Inc., a Nortek Air Solutions company. Multiple fans generate the 202,000 cfm required, but a modular design would allow individual fan cubes to be navigated through the building’s three-foot doorways and stacked in place. The resulting system would be more energy efficient and quieter than the existing fan, while also providing system redundancy.
“We looked at FANWALL TECHNOLOGY as a way to upgrade the system without having to bring in a whole lot of demolition equipment,” said Dennis Latta, construction manager for the Pyramid Center. “It was a good option because we could redesign the layout of the cooling coils, fan intake, and ducting at the same time.”
"The fifth-floor mechanical room is now quieter, more spacious and the multiple array of fans makes it easy to understand why it's unlikely we'll have a major disruption to cooling on floors one through 18."
Equipment
Fan Cubes Easy to Install in Limited Space
From the early stages of the project, Randy Scott, senior vice president, Critical Facilities Group, Skyline Construction, credits Nortek Air Solutions with being an active participant in the project. “Right from the start, Norman S. Wright was involved in the project and part of the team working with us on the complex logistics associated with the FANWALL implementation,” said Scott. That included a tour of the factory in Tualatin, OR, as well as pre-planning, installation, implementation, and follow-up.
Two of the primary challenges for the demolition and construction were to maneuver and install the new fan system, coils, and associated piping in the confined space of the mechanical room, and to do the retrofit project in stages on weekends so tenants would not be inconvenienced.
“The design challenge I had was to find a space for the new fan system, upstream or downstream from the old fan, so we could get it all set up ahead of time, and then determine the geometry of the space,” said John A. Oldham, P.E., principal of Oldham Engineering, Inc., the mechanical firm for the project. Oldham Engineering has worked on other mechanical engineering projects in the building for the last 10 years. “We had some difficult space to design in, and everything had to be measured ahead of time to the nearest inch — including height, width, conduit, pipes — so we knew everything would fit. We had the added advantage of being able to eliminate sound-traps altogether, because the fans operate so quietly. That opened up another five feet on either side of the old fan.” In fact, the entire FANWALL system only requires about five feet of space. That means all preparations could be completed while the old fan remained operational, virtually eliminating downtime for tenants.
Oldham had another priority as well. “I really wanted to get more static pressure into the space and make the whole system run a lot better. The building has had overheating problems since it was built. Before we found FANWALL TECHNOLOGY, we couldn’t fix that. We couldn’t change out the fans because they were buried too deep in the building, and the building couldn’t be down as long as it would take to replace them. With FANWALL TECHNOLOGY, the ventilation conditions are a lot better, and we’re saving a lot of energy.”
The demolition and reconstruction work, completed in three weekends per side, was the responsibility of Kevin Frederick, project manager for the mechanical contractor firm, Anderson, Rowe and Buckley, Inc., San Francisco. Oldham had found enough space downstream from the original fan, and that’s where new construction occurred.
“Over the first weekend, we installed and commissioned the new coils, leaving the old fan in place with new coils,” said Frederick. On the second weekend, the old fan was removed, and Frederick’s team installed the new FANWALL cubes. The old fan measured 12 x 12 feet and included a 1,900 pound motor and concrete base. It was removed between 6 p.m. Friday and 6 a.m. Saturday.
“Once the old fan was removed, installing the FANWALL system itself was just a matter of getting the cubes in place, bolting them down, assembling and flashing off to the existing plenum and the new plenum area, and commissioning,” said Frederick. “It was the easiest part of the project. We laid out the cubes on the floor and sequenced everything in the proper order to fit in the plenum correctly. It went together very simply.”
On the third weekend, the existing coils and filter bank were removed and the new filter bank installed. The sequence was the same for the second mechanical room. The entire demolition and reconstruction was completed in six weekends, three weekends per side.
“Given the complexity and dynamics of the project, I’d do it exactly the same way with the same players involved if I had to do it all over again,” said Chief Engineer Peterson. “It was that much of a home run.”
KEY POINTS
- Aging air handler fans in the Transamerica Pyramid needed to be replaced without disrupting tenants or interrupting normal operations.
- Building management wanted a system that would provide better energy efficiency and improved reliability.
- A modular fan system using FANWALL TECHNOLOGY met all project goals and provided additional benefits that exceeded expectations.