Stony Brook University Medical Center
Hospital Improves Reliability and Efficiency with Minimal Disruption to Surgery Center
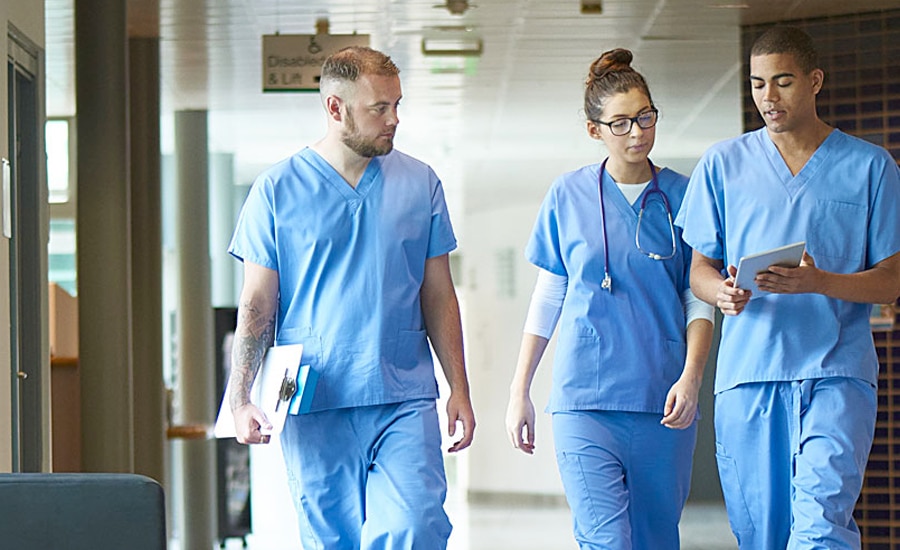
At A Glance
A medical, surgical and teaching facility to rival the best in the world! That vision was the impetus for a major Medical Center’s $300 million expansion and renovation project. What was once an ambitious goal beset by practical challenges is now a reality. Today, the Long Island, New York hospital ranks among the gold standard medical institutions in North America.
The greatly enlarged and renovated facility offers more than a visually attractive environment. It is also designed to be easy to navigate for patients, visitors, and staff. Open plan architecture with abundant natural light reflects the bright, positive attitude of caregivers. Surgeons now work in high-tech operating rooms that facilitate best-practices in modern medicine.
“The Knockdown Air Handler with a FANWALL array can be connected to existing ductwork, making it a cost-efficient retrofit. The auxiliary components are easy to install and, once assembled, the air handler delivers maximum energy efficiency and low noise performance.”
Equipment
FANWALL Redundancy is Key
The Knockdown Air Handler was built to meet requirements specific to the hospital. For example, the ideal temperature in an operating room is considerably lower than normal control temperatures. So the system featured two sets of coils, one for the base building system and a second set for the auxiliary chiller. This guaranteed redundancy in the chilled water system at all times.
The air handler that Ventrol custom engineered weighed 33,000 pounds, with a total of nine fans in the FANWALL array. The system was designed to operate under normal conditions with six active fans delivering a total 31,800 cfm., or 38,000 cfm with all nine fans activated.
Any buildup of surface condensation caused by a variance between ambient air and conditioned air can produce HVAC problems. Ventrol eliminated the possibility of such problems by building the air handler with hybrid foam thermal break technology consisting of fiberglass and foam with a R-18 value.
KEY POINTS
- A Knockdown Air Handler with a FANWALL array is used to replace an aging fan system.
- The Knockdown construction of the unit enables the project team to complete the retrofit in a tight timeframe.
- The FANWALL array increases system reliability.